Certificates
Kekkilä-BVB introduces sustainability roadmap for 2030
KEKKILÄ-BVB PRESS RELEASE 28.1.2020
Kekkilä-BVB has set demanding targets to become a net positive company by 2030, guided by our sustainability roadmap with eight concrete targets. One example of Kekkilä-BVB´s sustainability actions is to launch products containing sphagnum moss for professional growers and retail customers.
“It is quite natural for horticultural companies to talk about sustainability, since we are all contributing in making the world a greener place one way or the other. But that is not enough. It´s all about how we do it”, says Juha Mäkinen, CEO of Kekkilä-BVB.
Kekkilä-BVB became the leading horticultural company in Europe after Finnish Kekkilä and Dutch BVB Substrates joined forces.
“With big size comes also big responsibility. It is our obligation to promote biodiversity and to participate in preventing the effects of climate change. We have taken the stand to be a promoter for sustainable horticultural business and to enable our customers to meet their sustainability goals”, Mäkinen says.
Sustainability roadmap steers actions
Kekkilä-BVB´s sustainability work is guided by a sustainability roadmap. It consists of four focus areas with measurable targets. These focus areas are related to the wellbeing of people in the value chain, creating sustainable new innovations for food production and living, promoting circular economy and enhancing biodiversity.
“Concreteness is very much needed in sustainability work. This was a very clear message both from our customers and personnel when we made our sustainability roadmap. One way to add concreteness is to openly measure the negative and positive impact. This is why we are participating in Growing Media Europe´s work in calculating LCA (Life Cycle Assessment) for different growing media materials. This builds the base for the sustainability standard for the European growing media industry”, concludes Mäkinen.
From talk to action
An example of Kekkilä-BVB´s sustainability driven business approach is the launch of substrates containing sphagnum moss at the global horticultural fair, IPM Essen.
Sphagnum moss grows on top of the peat bogs and has not started to decompose like peat. As a living material it regrows relatively quick. Less water is needed for crops grown with sphagnum moss, since it has a large water holding capacity. Tests have also shown excellent growth results.
“To ensure our customers’ success and that the growth results are optimal, we have done extensive tests before launching our products with sphagnum moss. We see that as part of our responsibility.”, adds Mäkinen.
Since sphagnum moss is a novelty raw material and acts differently than peat, it is not yet RHP (quality mark for substrates) certified. Kekkilä-BVB is co-operating with RHP to have it certified according to RHP´s standards.
Read more about Kekkilä-BVB´s concrete sustainability cases here: kekkila-bvb.com/sustainability
Contact:
Juha Mäkinen, CEO, Kekkilä-BVB: juha.makinen@kekkila-bvb.com, tel. +358 40 046 4549
Nina Kinnunen, Director, Sustainability, Brand and Communications: nina.kinnunen@kekkila-bvb.com, tel. +358407775333
Retail
Alternative casings and a sustainable mushroom industry
Mushrooms are a low-impact food. As vertical farms, their land footprint is small, and energy and water inputs into mushroom crops are much lower than comparable foods. Consequently, mushrooms have an excellent CO2eq rating. This ‘green’ image, coupled with great taste and an ever-growing list of health benefits, weaves a sweet narrative of mushrooms as a sustainable food source for a growing world population.
There is just one little snag:
Casing, or more specifically, peat casing.
Peat extraction, its history, ecology, the debate around sustainability, and its application in the horticultural industry could fill pages. What is relevant is that the UK, Ireland and Germany, major peat suppliers, are considering phasing out peat extraction. And although there is currently sufficient supply of peat for the horticultural industry, sustainable alternatives are needed to future proof the mushroom industry.
As a country without peat extraction, Australian growers have relied on expensive imports from Europe. Development of an alternative casing from local materials would potentially save cost, avoid shipping delays, and enhance the sustainability of the mushroom industry.
Presentations at the AMGA conference from Folkert Moll (Kekkilä BVB) and Dr Ralph Noble (Microbiotech Ltd) showcased the latest developments in Europe, where much of his research is occurring.
Key sustainability trends impacting the industry
The mushroom industry is not immune to global events, whether they be social, economic, or environmental. Wholesalers and retailers are acutely aware of the impact of sustainability on brand values and scrutinise supply chains accordingly.
Provenance claims, whether a diamond, a bottle of wine, or a mushroom, no longer start and end with location; the full supply chain is part of the story, including any raw materials, used in production.
So where do you start? Folkert Moll, the sustainability manager at Kekkilä BVB, brought all this it into clear context for the mushroom industry. To navigate a path to sustainable casing, his company is looking to the UN Sustainable Development Goals1 as a guide. Six key development goals impact the mushroom industry particularly, namely urbanisation, climate destabilisation, ecosystem decline, food crisis, inequality, and resource scarcity.
Resource scarcity is the immediate focus, including:
- Availability of local and circular raw materials
- Competition with other substrates and industries
- Quality of available raw materials and processing needs
- Upscaling from research to commercial application
So, what makes a good casing material?
The holy grail of an alternative casing, simply put, is a material that is as good as peat but with a lower environmental footprint. Each raw material has pros and cons, and chemical, physical, and biological properties need to be well understood. Further, these properties can change when materials are mixed.
Specific characteristics include:
- high-water holding capacity
- low salt content
- hostile to moulds
- low cost
- readily and reliably available locally
- does not stick to mushrooms
- no pathogens or contaminants
- does not attract flies
New solutions
According to Wageningen University in the Netherlands, the volume of growing media will need to increase by 332% over the next 30 years to meet the food demands of a growing world population.
By 2050 the amount of new raw materials (not yet commercially in use) has to equal the total amount of raw materials currently used for growing media. This already huge challenge is compounded by the competition for resources from other industries.
Demand for peat will likely double, although this largely depends on the political trade-off between the role of peat in enabling food safety and security, and the environmental impact of extraction. It is important to note that as horticultural peat extraction accounts for only 0.05% of global peatland use, and restoration efforts often add value to otherwise degraded peat ecosystems, the environmental impact is small.
Nevertheless, to ensure a sustainable and prosperous mushroom industry, the development of alternative casings is an industry priority.
One such group that has taken on this challenge is the European consortium BIOSCHAMP, a collaboration of six countries to research, mix and test new circular raw materials and biostimulants that can improve sustainability, while ensuring the safety and effectiveness of mushroom growing.
The consortium aims to create novel casing soils using new materials with key qualities that include appropriate gas exchange, mycelium protection, excellent water holding capacity, nutrient holding capacity and are free from pests and pathogens. It also needs have suitable physical properties, including a structure that supports and protects the expanding mycelia without being a barrier to growth.
“We (Kekkilä-BVB) joined as a project partner two years ago with a goal to create a more sustainable casing soil, reducing the sector’s dependency on peat,” Folkert said. While the research is still at the trial stage, preliminary results are promising. In Figure 1 materials are not identified, but those marked with ‘✓’ provided results statistically similar to the reference peat.
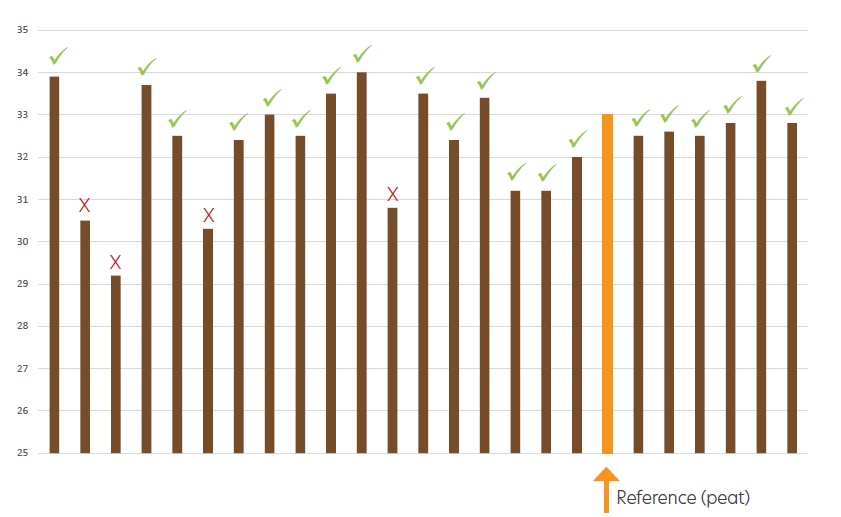
Figure 1. Yields obtained using alternative casing materials (kg/m2), X denotes materials where yield was reduced; most materials tested were not statistically significantly different to peat, marked with a ✓.
“By 2024 we will be able to discuss the alternatives in more detail, but in the meantime, I feel very optimistic that a solution is not far away,” Folkert said.
The materials were also assessed for their effects on disease, specifically number of mushrooms with bacterial blotch and occurrence of visible Trichoderma. Several materials performed as well as peat on both counts (Figures 2 and 3). Combining these results with yield data reveals several materials worth taking to the next stage of testing.
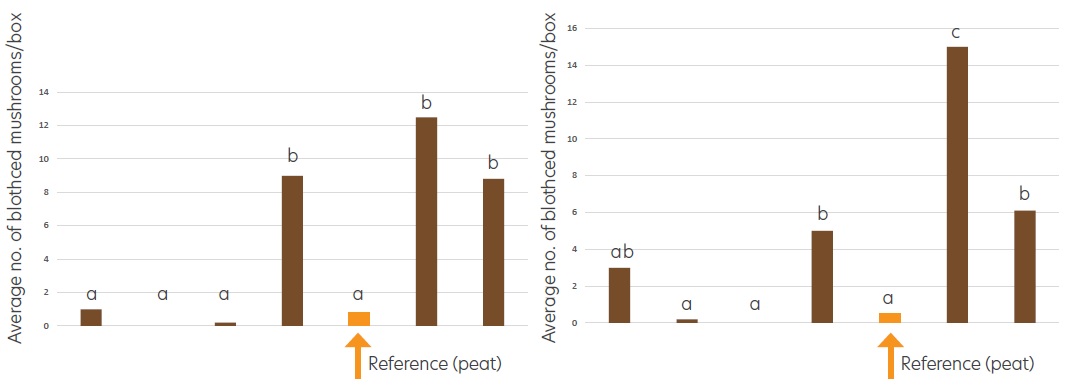
Figure 2. Bacterial blotch measured in average number of blotched mushrooms/box. Materials marked with ‘a’ are not significantly different to peat.
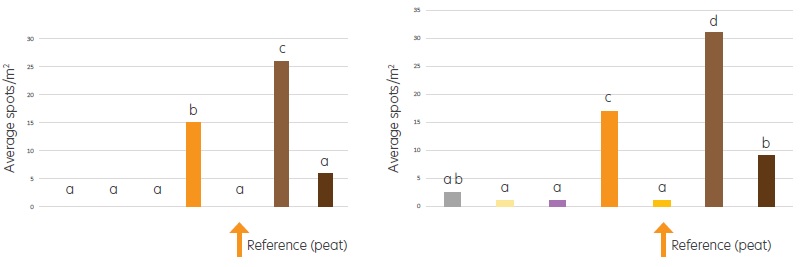
Figure 3. Green mould measured in average spots/m2. Materials marked with ‘a’ are promising.
What’s happening in the meantime?
While researchers toil away finding a fit for purpose peat replacement, peat will continue to be the major constituent of mushroom casing. Kekkilä-BVB are committed to the best possible practice (following Responsible Peat Production guidelines) in the sourcing, extracting, and rehabilitation of peat landscapes. which are extremely high in Sweden and Finland, where most of the peat is sourced.
Understanding Microenvironments to choose the right alternative casings
Is blending peat with something else the answer? Probably not, says Dr Ralph Noble, who has been researching the microbiology of mushroom cultivation for over 40 years. Dr Noble has turned his attention to how understanding the microenvironment of casing can help us achieve net-zero, peat-free mushroom farming. Dr Noble’s presentation focused on the properties of casing and factors that impact yield, quality, and disease.
Some background
Researchers have been searching for alternatives to peat for many years.
Dried milled peat was used in Australia up until the early 1990s, when wet dug peat became more readily available. Although the wet dug peat is bulkier and heavier, its superior water holding capacity meant it quickly became the preferred material. This is because it retains the porous structure of the Sphagnum moss from which it was formed.
Other countries are already trying to reduce use of peat, either due to cost or from necessity. For example, France and Spain commonly mix clay from local soils with peat, while China still uses milled peat, sometimes combined with rice husks and river mud.
However, it is hard to beat peat. South Africa has minimal sources of peat locally, and those it does have are protected from extraction. During the
years of apartheid, sanctions made it impossible to purchase peat externally. Local research developed and commercialised a product based on sugar cane bagasse. While this was widely used, the end of restrictions has seen farms return to the best possible casing material –wet dug moss peat.
Many options have been investigated, each with their own pros and cons, as illustrated in the table below this article (Figure 4.)
What has the science said?
If science is the process of asking nature a question, then data is her answer
Luckily for the mushroom industry, Dr Noble has been asking the right questions and has collated some useful data to answer the original question: What works and why.
When considering yield alone, peat mixed with up to 25% other materials often looks promising. Unfortunately, yield often declines as the non-peat portion increases past this level.
Some of Dr Noble’s data is shown in Figure 5. In these trials, only recycled rockwool and bark plus green waste compost could be added to peat as 25% of the total volume without negatively affecting yield.
“I don’t think the answer is in blending peat with other materials,” commented Dr Noble. “A full replacement for peat is a better option than simply trying to reduce it as a component of the mix.”
When examining potentially useful materials, it is important to consider not just water holding capacity (WHC) when saturated (e.g. after heavy watering), but also how the materials hold on to this water to slow down losses caused by evaporation and drainage.
Wet dug peat is an ideal casing because it has a high water holding capacity when saturated, and holds on to this water so that little drains out. This leaves a good supply of water for mushroom mycelium between waterings. Although wood fibre holds about 80% water when saturated, most of this is released when only a small suction is applied. On a mushroom bed, the water in wood fibre readily evaporates and drains out, leaving less for the mycelium to extract.
Conversely, green waste compost holds only 60-70% water when saturated meaning that it has to be watered frequently with smaller quantities. However, it holds on to this water better than wood fibre does when a suction is applied. The material dries out more slowly on a mushroom bed leaving a supply for the mushroom mycelium to extract.
The capacity of materials to hold water is mostly influenced by pore size, and the ability to hold water at different suctions by having a range of different pore sizes within the material or blend of materials.
Sphagnum moss, preserved as wet dug peat, has an ideal natural range in pore sizes. Avoiding excess mechanical agitation preserves this structure. However, other materials may actually benefit from mechanical intervention to improve blending of materials with large and small pore sizes (e.g. bark and clay).
Other issues to consider
Mushroom cultivation is not just a matter of producing high yields, other cropping factors must also be considered:
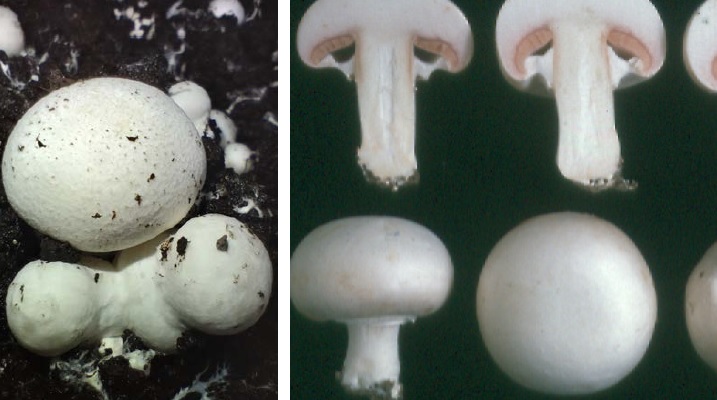
Material stuck to mushrooms (left), leggy mushrooms (right)
- Some materials are sticky and will cling to the mushrooms
- Some casings produce leggy mushrooms
- Over pinning can be a problem – high yield but small mushrooms
- Case run can be slower with alternative casings, increasing the time taken to grow a crop
- Irrigation practices are likely to need to change
Overpinning (left), slow case run (right)
- Risk from Trichoderma (green mould) is increased when peat is blended with other materials.
Green mould (Trichoderma harzianum) on 25% bark casing
- Some organic alternatives can also increase the risks from sciarid flies
- Conversely, bacterial blotch is reduced in some peat-based blends
Dr Noble is optimistic. Despite a few challenges, we are not too far off a peat-free future, and he wagers that by 2030 Australia will be producing high yields of quality mushrooms without peat casing.
We look forward to following the results of his work as it becomes clearer what those alternative casings might look like.
Material | Advantages | Disadvantages |
---|---|---|
Wet dug peat![]() |
Free of pests and diseases Low pH and nutrient content Excellent water holding capacity Appropriate pore size, allowing air to reach mycelia Low bulk density Structurally stable and supportive |
Not sustainable due to slow regrowth of peatland (<1mm/year) Long travel distances = high freight costs Biosecurity restrictions lead to import delays Hard to re-wet if it dries out |
Coir![]() |
Renewable and readily sourced within the region Good structure and stability Good water holding capacity Appropriate pore size Easy to re-wet after drying Low bulk density |
Must be leached to reduce salt content, requiring large volumes of water Risk of contamination (pests, diseases and chemicals) Imported, increasing freight costs Competition from other users affects price and availability |
Spent mushroom compost![]() |
Available on farm; solves disposal problem so cost-positive Good water holding capacity Appropriate pore size Good structure and stability |
High salt content – must be leached before use, requiring large volumes of water Must be heat treated to eliminate pests and diseases |
Recycled casing![]() |
Available on farm; solves disposal problem, cost-positive! Reduces issues with salt content in spent mushroom compost Can be added up to 1/3 without affecting yield |
Equipment needed to remove casing from spent compost Must be heat treated to eliminate pests and diseases Does not eliminate peat from growing system |
Composted wood fibre![]() |
Renewable and locally sourced High porosity Water taken up but easily lost through evaporation and drainage Low bulk density Structurally stable |
May increase requirement for added nutrients Can become compressed Likely to require leaching or steam treatment before use Susceptible to green mould |
Green waste compost![]() |
Readily locally available Inexpensive Moderate water holding capacity and retention Appropriate pore size May suppress some pathogens |
Variable characteristics, depending on substrates used and composting process High nutrient content (K and P) Potential for high salt content Risk of contaminants (pesticides, microbes and physical) Must be blended with other materials Relatively high bulk density |
Composted bark chips![]() |
Readily locally available Inexpensive Large pore size |
Low water holding capacity May require leaching before use Risk of contaminants, especially if not composted correctly May contain organic compounds that inhibit growth |
Rockwool![]() |
Pest and disease free Inert and structurally stable Free of nutrients Good water holding capacity Appropriate pore size and range Low bulk density |
Expensive – energy intensive production process plus high freight costs Low buffering capacity Can be hard to re-wet |
Used rockwool![]() |
Readily locally available Potentially inexpensive Neutral pH and low in nutrients |
Requires processing and granulation before use Limited availability |
Vermiculite![]() |
Pest and disease free Inert and structurally stable Free of nutrients Large pore size Extremely low bulk density |
Expensive – energy intensive production process plus high freight costs Relatively low water holding capacity |
Paper and cardboard waste![]() |
Readily locally available Inexpensive High water holding capacity |
High bulk density Source of contaminants Can encourage mould growth |
Clays and other by-products from mining![]() |
Materials may be readily available (some areas) Potentially inexpensive Potential yield improvement (coal tailings) Moderate water holding capacity Generally inert with stable structure Low risk of pests and disease Positive trial data exists |
High bulk density May dirty mushrooms Can adversely affect casing conductivity |
Original article by Dr Jenny Ekman and Paulette Baumgartl, published by MushroomLink (Australia) in their magazine January 2023.
Kekkilä-BVB improves environmental impact with circular economy products
In this series of articles, we show how Kekkilä-BVB promotes the circular economy. In this first article we put the role of soil in the circular economy in the spotlight. We consider what sustainable soil really is and explain how we create growing media in our journey toward a circular economy.
The European Union’s goal for 2050 is to be a society based on a circular economy, for Finland it is even 2035. In a circular economy, all kinds of waste and wastage are reduced: Goods are made to last longer and raw materials are kept in circulation, for example by recycling materials and reusing products for different purposes. Overconsumption is reduced, goods are repaired more than at present, and the joint use of products is increased.
Circular economy is a modern word, but there is old wisdom in it. The current kind of waste and use of disposables is actually quite new for humanity. The circular economy is about valuing and cherishing things and raw materials. This is important, because natural resources are used in the world well beyond what one earth is enough for.
A sensibly implemented circular economy curbs climate change and loss of nature, but society’s security of supply and resilience also increase when materials are used again and again locally.
In order to move to a more sustainable base than the current one, European countries have implemented strategic programmes for the circular economy. The implementation of these programmes always requires the involvement of society as a whole. In this article series, we explain in more detail how Kekkilä-BVB participates in the implementation of common circular economy goals.
Growing media that save natural resources
Let’s start with the growing media. In order to grow, plants need a suitable substrate, to which they can attach their roots and from which they can take water and nutrients. When looked at better, the growing medium is a kind of soil made from a mixture of different raw materials. Together, they bring a suitable structure to the soil, i.e. for example the right amount of airiness, nutrients and water-binding capacity.
Kekkilä-BVB manufactures growing media for many uses. For consumers, we sell products pre-packaged, but for the needs of landscaping, such as urban green areas, parks and roadsides, we often prepare the growing mediums according to the customer’s needs and delivered to the destinations per truck. In addition, Kekkilä-BVB manufactures growing media for professional growers in gardens and greenhouses.
We have improved the environmental impact of growing media by introducing new, rapidly renewable raw materials and effectively transitioning to a circular economy.
Compost – nutrient-rich recycled raw material
One of the most important raw materials for soil are various composts. Kekkilä-BVB produces its own composts at its own composting plants in Finland. At the plants, we transform various types of organic waste into growing media.
For example, at Teuva’s facility in South Ostrobothnia in Finland, we collect and compost green plant waste from greenhouse growers in nearby areas, i.e. spent growing media, plant stems and leaves. That way we produce high-quality green compost, which we then use as a raw material for soil. This recycled raw material is used both in large landscaping projects as well as in products sold to consumers.
Kekkilä’s composting facilities also compost biowaste from municipalities and companies. We use this to make growing media for the needs of landscaping.
For example, in Finland, the Nurmijärvi composting plant receives biowaste from consumers and shops from nearby municipalities, various types of sewage sludge and various organic side streams from local industrial plants. These all get a new life through processing and composting, for example as tree substrate in parks or in the soil roof gardens.
The production of the raw material for growing media in this way is already fundamentally sustainable. This way we put biowaste to good use, instead of it taking up space in landfills and producing greenhouse gasses as it decomposes there. In addition, using waste streams locally reduces transport and the related emissions. The use of different composts in growing media also significantly reduces the need for mineral fertilizers, because green compost is very nutrient-rich and its microbial activity is high.
Local materials for soil
Unique properties of peat
We also need other components for a good, high-quality growing media. Peat is traditionally a widely used growing media material, because it is abundant in Nordic and Baltic countries and its properties are unique. It is a pure natural material with no weed seeds or plant diseases. Also, peat has excellent water holding capacity and naturally contains substances that promote plant growth. Due to this we use it both in potting soils sold to consumers, as well as in substrate mixes intended for landscaping. Additionally we can add it to the growing media for professional growers.
Since the climate effects of peat harvesting are significant, it is wise to reduce its use.
Kekkilä-BVB is constantly developing more different raw materials for growing media and, for example, has just launched a completely circular growing medium for consumers in Finland and Sweden. In addition to green compost, this soil is made from domestically grown moss and wood fiber.
Wood fiber made of waste wood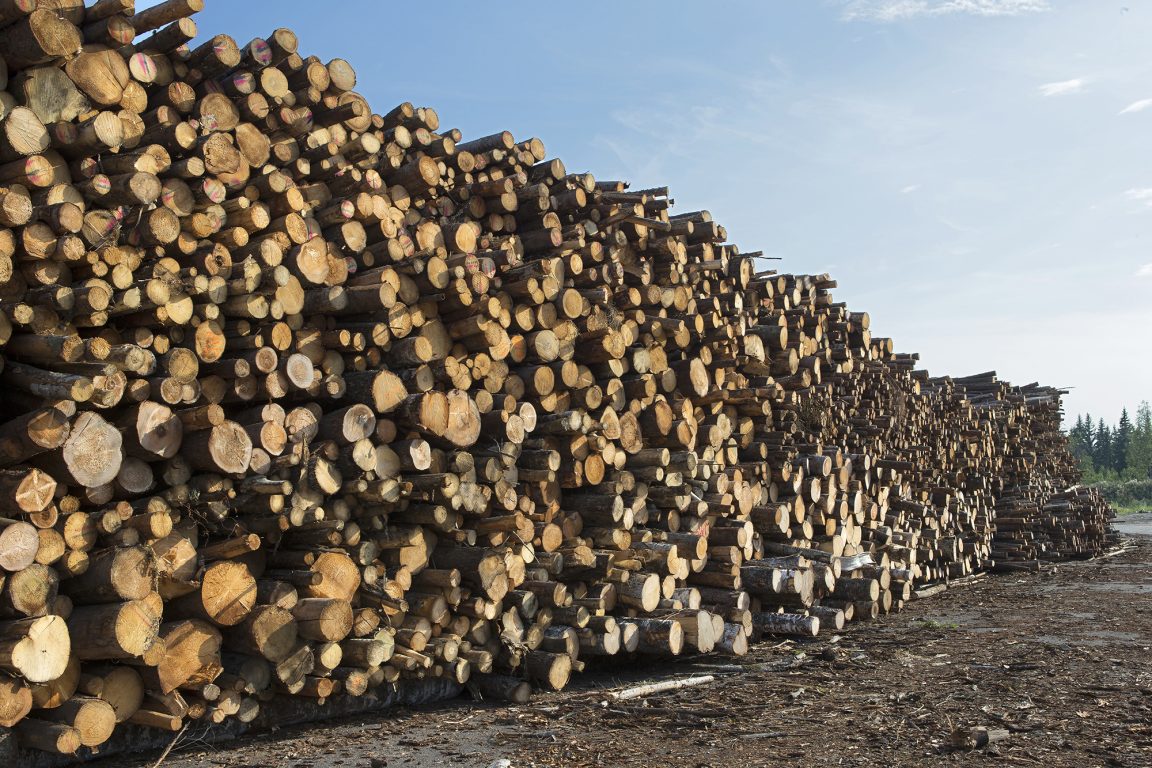
In Parkano we make wood fiber from wood that has accumulated as a byproduct of harvesting from peat production areas. We can also make the fiber from many types of leftover wood and thinning wood.
The wood fiber is chopped from leftover wood on the new bio-fiber line of the Kekkilä-BVB Parkano factory. Kekkilä-BVB has invested in a line that makes it possible to manufacture new kinds of recycled products.
It is a good growing medium material as it is natural and light and can be made from raw materials available nearby. From the point of view of the plants, the fiber brings porosity to the soil mixture, which is important for the development of the roots.
Fast renewing moss
The third component of this circular growing soil is moss, which is excellently suited as a substitute for peat. Moss also renews itself faster than peat, about one centimeter per year, and its climate emissions are less than a fifth of peat emissions. After the moss is harvested, the species regenerates quickly, as long as the moss is not harvested too deeply. Moss can also be cultivated, for example, in former peat production areas. The availability is currently limited and we are researching how to increase supply.
“Taking responsibility means innovating and balancing value choices.”
The many dimensions of sustainability
Moss, peat and wood fiber used in growing media are returned to the natural cycle as natural materials. Some we first reuse as part of economic cycles: for example we collect peat-based growing media from professional growers in Finland to the Teuva composting facility. There we process it into raw material for new soil.
However, no material, whether degradable or renewable, comes from a vacuum: all raw materials have some kind of effect on the surrounding world. That’s why the use of raw materials means continuous monitoring, reflection and evaluation of the effects.
For example, the collection of moss affects the local nature. Also its repair requires a lot of surface area if the use of moss becomes significantly more common. Moss grows about one centimeter per year. Therefore a maximum of 30 centimeters is collected from one area every 30 years. The moss cover renews itself when it is harvested, taking care of the continuity.
Sustainable moss harvesting
Our parent company Neova has developed sustainable moss harvesting practices and processing for several years already. And, together with other operators in the field, it has drawn up work instructions for sustainable moss collection.
Kekkilä-BVB only accepts for its products moss grown and collected according to the principles of sustainable collection. The moss used by Kekkilä-BVB is also always certified with quality and environmental certificates (ISO 9001 and ISO 14001).
The suitability of moss for use as a growing medium has been studied in Kekkilä-BVB for a long time, because with the help of this moss it is possible to reduce the use of peat.
Other materials in growing media
Many materials are sustainable and renewable in themselves. However how much we use them, and which other material’s place they fill, affects the level of sustainability. We use, for example wood, together with other raw materials in addition, to create growing media. However there is fierce competition for many materials, including side streams and waste. Also the energy crisis has tightened it even more. Therefore several side and waste streams, that we could have been using for the production of organic raw materials, are now also used for burning for energy.
It depends on the situation when a certain use is the most sustainable. For example, coconut fiber is sometimes used to replace peat in growing media. But how reasonable would it be to build the cultivation of domestic plants on top of global dependencies? And how will coconut plantations and shipments affect the balance of nature if the need for coconut continues to grow?
Choices are not one-off, and they are always value choices as well.
At the core, quality and locality
We find locality an important value. In these times, the importance of this is emphasized. Peat is a domestic, excellent, valuable raw material that cannot be completely replaced yet. We research new domestic materials, and take effort to put them into full use as soon as possible.
At the same time, quality is at the core of sustainable and responsible operations.
Nurturing of the value of raw materials is the core of the circular economy, and it also applies to growing media. We take careful responsibility of using raw materials, use them to make high-quality products tailored for different uses. Whereby we ensure plants grown in our substrates grow as well as possible.
For each plant, the optimally chosen growing media has the right fertilizer balance, pH, porosity, water retention and water movement, it is full of microscopic life and tolerates different weather conditions. The high-quality product also keeps well in its packaging on the way from the factory to its destination. So a new green life can sprout in it, which as it grows binds carbon and produces oxygen and above all creates well-being that continues to spread.
In the next part of the story series, we will tell you what kind of material cycles Kekkilä-BVB implements in landscaping and composting plants. Kekkilä-BVB’s strengths in the development of cycles are networking and long experience with materials and their testing.
This article is based upon a posted article by Kekkilä Garden.
Responsibly Produced Coir: A key material for growing media
In our search for renewable raw materials in growing media, we often encounter the suggestion to simply switch to coir (also known as coco). While this seems straightforward, our exploration using the Sustainability Compass reveals that coir, as a material, next to being a renewable and good alternative, it also presents its own set of challenges. Producing “Responsibly Produced Coir” requires attention to the social responsibility of the harvest and the processing of coconut fibres, as well as the water conservation aspect.
Social Responsibility
We’ve partnered with a select group of coir companies that share our commitment to sustainability. To us, sustainable business means fair treatment of workers, along with their health and safety. Our coir suppliers are required to adhere to our Code of Conduct and obtain SEDEX or SA8000 certification. We also make site visits to verify that our high standards are being met in practice.
Water Conservation
Coir is known for its excellent structure, stability, and re-wetting capacity, contributing positively to a good air/water ratio conservation in growing processes. However, post-harvest, significant water is needed for cleaning and buffering coconut fibres to make it suitable as a growing medium. This is a critical step to remove contaminants and reduce salt levels. The water-intensive nature of this process is a concern, especially in regions where clean freshwater is scarce.
Responsibly Produced Coir (RPC): Similar to the RPP certificate for Responsibly Produced Peat, we’re collaborating with the same foundation and other companies to establish a standard for Responsibly Produced Coir. This initiative underscores our dedication to environmentally conscious practices that balance substrate quality with planetary well-being.
For more information contact Folkert Moll () and Berry Mauritz.
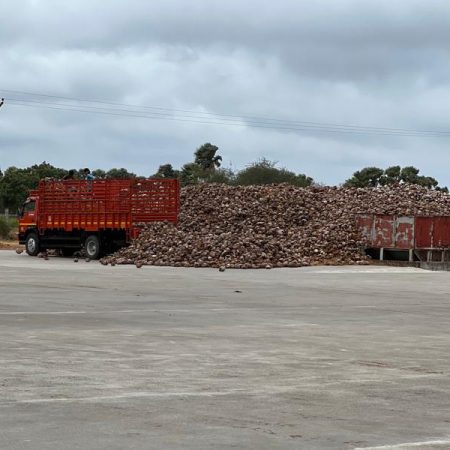
Coco shells are collected from plantations and transported to the factory site.
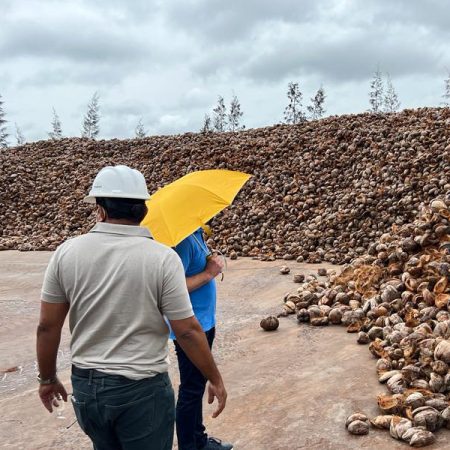
They are stored for 2-3 months before getting processed.
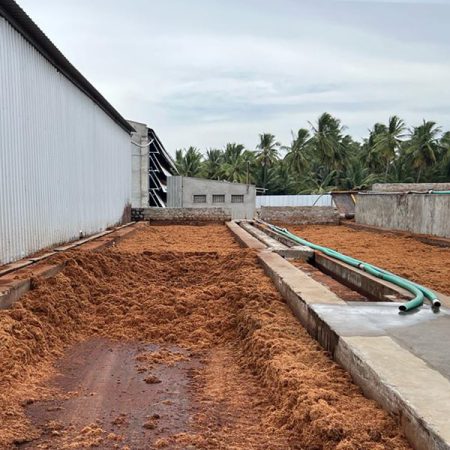
The coco peat is being washed.
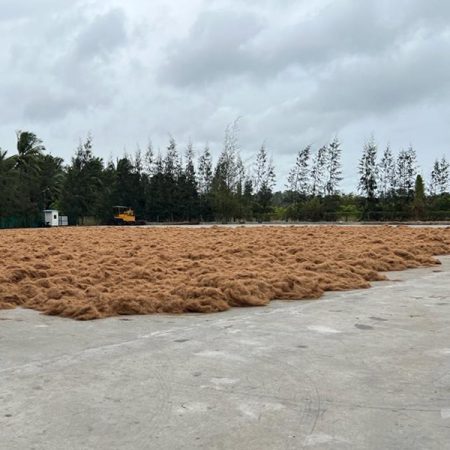
Cocofibres are spread out on concrete floors for drying purposes.
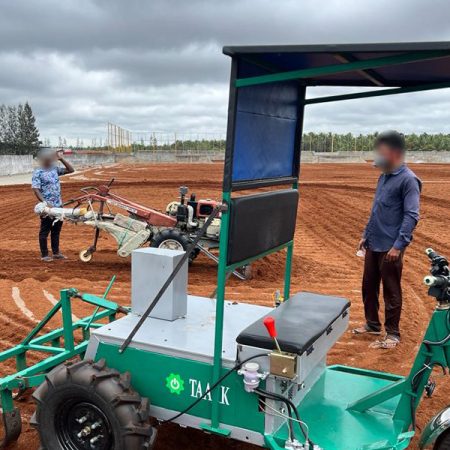
The coco peat is turned, to dry outside in the sun. The more modern electric turner in the front and older model in the back.
Grow21 Speakers
Grow22 – Join us to make a difference
“Sharing knowledge put’s the customer in the driving seat”
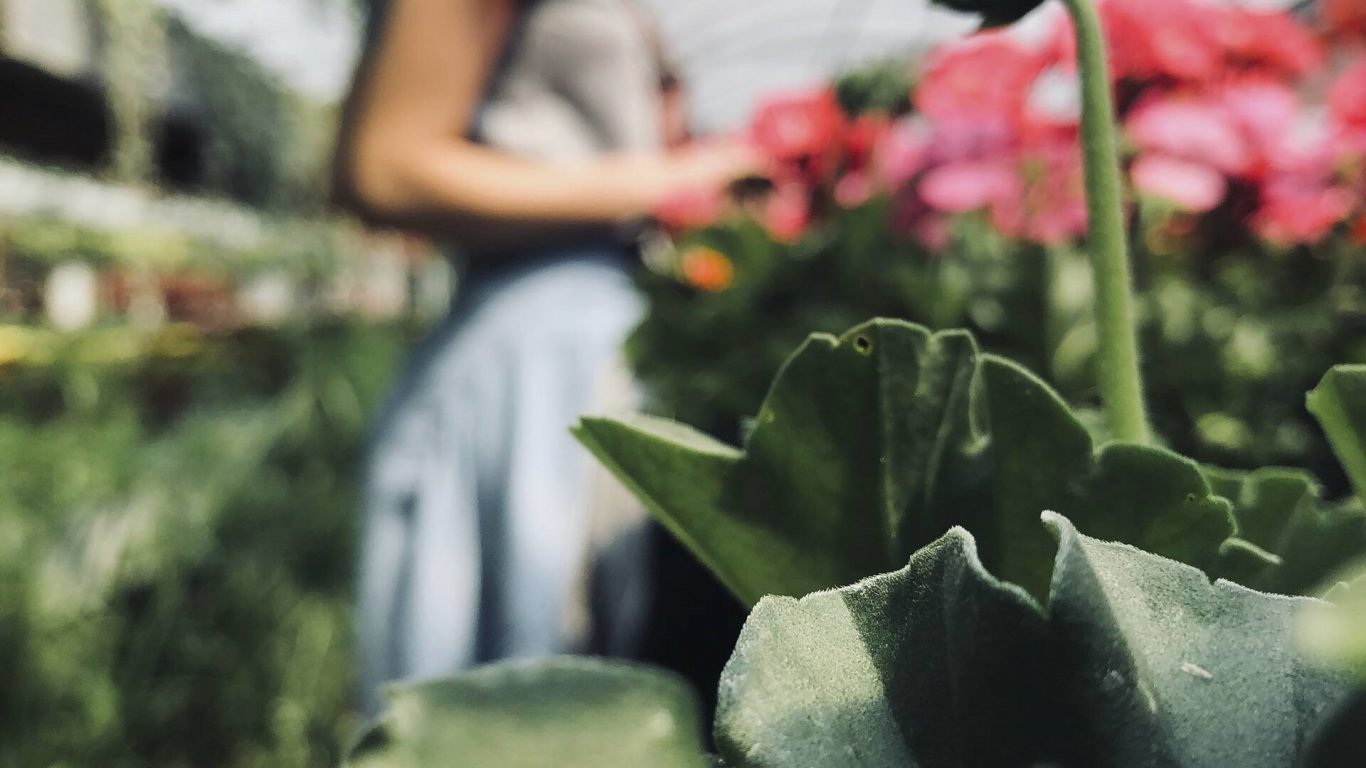
Garden Center
As a leading supplier of potting soil to garden centers, food retailers, and DIY chain stores Kekkilä-BVB knows how the buyer’s journey has changed over the past years. Today, the demand for innovative Private Labels beside branded products is high and brings both manufacturers and retailers to a new level of co-creation.
Buyer´s journey is all about building partnerships
For Kekkilä-BVB Retail, who offers private label products as an extension line to the branded products, insight into buyers’ journey is all about sharing knowledge and building partnerships with customers. The history of Kekkilä-BVB lies in professional horticulture and goes back some one hundred years. Today it is one of the largest global players and Retail benefits from this professional horticultural experience.
Sharing knowledge
Talking to Rein Donselaar, Sales Manager Kekkilä-BVB, customer relationships are all about sharing knowledge. Kekkilä-BVB has an extensive network of internal and external data insights about products, trends and segmentation providing customers with in-depth market knowledge. Rein describes it as a process where Kekkilä-BVB, together with the customer, take control over the product and design their own recipe, tailored to the needs of the consumers. To Rein, sharing knowledge is all about giving customers the control over quality and price.
– With its twelve production plants and three laboratories, Kekkilä-BVB offers customers a world of knowledge, Rein says.
Brand positioning
But, how to position private label products and branded products in a successful combination? According to Rein, choosing a private label strategy is a matter of differentiating from competitors. Garden centers, chain stores and food retailers often use a three-step price strategy; budget, private label and branded products. Nowadays even premium private labels are being introduced.
“We help customers with positioning in terms of price point, quality, brand promise, placement against their brands and sustainability etc. We produce what our customers ask us to do. Going for budget or premium private label depends on their strategy. Together we shape the right recipe tailored to the customers’ brand promise”, Rein says.
If needed, Kekkilä-BVB also helps with the design of the private label, whether it’s a new innovative look or designed according to the customers’ brand book.
Combining a digital experience with instore choices
In the future, Rein foresees a world where the retailers are the experts and guide consumers step-by-step to the garden of their dreams, in a balanced online and offline setting. For instance, digital solutions like Google Earth makes it easier to look into a garden and help design it based on consumers’ wishes. A combination of online experience with instore choices like plants, flowers, pots, garden furniture, pavement choices, etc. will be the key to success.
– The retailers are the experts and a source of knowledge about how the online and offline world interact towards consumer behavior. The more the retailer knows about his product the more he can help customers to good choices, Rein says. “That’s why we share our knowledge with our customers”.
Text: Louise Harvig Olsmar
👉 Read more! What is peat and what makes it a great constituent as growing media?
To receive the white paper, enter your contact data so that we can send you a download link. Your data is safe with us.
Request our peat package
Kekkilä-BVB and Lidl – a customer case
Lidl asked Kekkilä-BVB for a universal potting soil ‘best in class with outstanding quality whilst being very sustainable’. Competition amongst the discount stores is high and Kekkilä-BVB designed six sustainable recipes of a very high quality and made a completely new packaging design, tailored to a young and urban audience. Kekkilä-BVB even gave Lidl the ability to offer an app were consumers get potting soil advice whilst scanning a plant in a Lidl store. This premium label called Earth Senses is specifically designed for Lidl and is available in various countries.
‘We expect the general market outlook for growing media to remain positive’
This article was published originally by FloraCulture International in their Digital magazine, May 2024 edition. Author: Timo Taulavuori.
FloraCulture International encourages the pursuit of joint activities in areas of mutual interest with national, and international societies, and organisations. Agreements have been reached between FCI and leading growers and trade associations worldwide.
Kekkilä BVB has 100 years of experience in growing media, particularly in peat. FCI magazine interviewed the company’s CEO, Pekka Tennilä, over coffee.
Since its founding in 1924 to meet a growing demand for fertilisers, Kekkilä has established a unique position in Finland as the country’s first company to introduce bagged potting soil to the amateur gardening market in 1952. That same year, the company launched a universal water-soluble fertiliser, Kekkilä’s Pink, which is still a firm favourite among amateur gardeners and professional growers. Since then, the company has grown over leaps and bounds, also making its mark in the manufacturing of bespoke substrate mixes for landscaping.
At the turn of the millennium, Kekkilä embarked on an internationalisation strategy that would see the opening of a branch 20in Sweden, where it acquired growing media manufacturer Hasselfors Garden. One year earlier, in 2019, the company reached another milestone when it joined forces with the more than hundred-year-old Dutch company BVB (Bas van Buuren) Substrates.
On 4 December 2023, the board of Neova Oy, of which Kekkilä-BVB is a subsidiary, appointed Pekka Tennilä, M.Sc., as CEO of Neova Oy and Kekkilä-BVB. Tennilä served as CEO of the alcoholic beverage company Anora from 2014 to 2023. During Tennilä’s tenure, Altia and Norwegian Arcus merged, forming Anora, a company listed on the Helsinki Stock Exchange. Before Altia, Tennilä held numerous key positions at the brewing company Carlsberg.
FCI magazine: In which countries do you operate?
Pekka Tennilä: “Today, Kekkilä-BVB is Europe’s largest manufacturer of growing media and exports products to professional greenhouse growers in more than 100 countries. It offers products and services to landscapers and consumers in the Nordic countries and Central Europe. Kekkilä-BVB has sales offices in 10 countries. Products change hands either directly or through authorised distributors and dealers worldwide. In Europe, Kekkilä-BVB has 13 production facilities, including two in Finland and Sweden, one in Estonia, one in Germany, five in the Netherlands and one in Italy. There are also four composting facilities in Finland. Our research laboratories are located in the Netherlands, and all production facilities have their own quality control laboratories. We also have two loading ports, one in Germany and one in the Netherlands.
What is the state of the global growing media industry?
Resource efficiency is at the centre of attention in farming and horticulture. This is due to an increasingly sustainable mindset and economic factors. This development supports the sale of growing media that save water and nutrients. Farming techniques are also developing, and agtech, greenhouse automation, and robotisation are gaining traction. The demand for substrates of uniform quality is increasing. Farmers are also keen to trial different raw materials to add to their substrate mixes, while product development worldwide in collaboration with farmers has taken on an even more significant role. The good experiences of the pilot farmers easily persuade others to try new solutions, mainly when they see that their pioneering peers produce better crops and, at best, also reduce their environmental impact.
What would you say are the biggest challenges and opportunities?
Climate change impacts arable cropping and growing seasons, increasing the need to grow in controlled environments. Many megatrends also impact our work. For example, urbanisation forces growers to produce food and flowers close to consumers, while restrictions on the extraction and use of growing media from an environmental perspective are also at stake.
Challenges include a surge in protectionism worldwide, disruptions in the global supply chain, and a growing anti-peat sentiment and legislation. But this situation also offers opportunities. Protectionism increases the demand for local. Kekkilä-BVB has invested in local farming trends for years because of the sustainability aspect. Supply chain disruption also asks increasingly for local logistics solutions. There’s ongoing research into new locally sourced raw materials that can contribute to a circular economy.
Peat continues to be an important raw material. But it is equally important to have a public peat debate, only if it is to clarify the difference between peat used for horticulture and peat used for energy.
Peat is part of Finnish core competence. How do you see its future role in growing media?
Raw materials based on the circular economy have been developed to complement and replace peat. Kekkilä-BVB does continuous research with both customers and scientific institutions to achieve the best growth results, as well as when using new/substitute raw materials such as coconut, moss, reed canary grass, green compost, and wood fibre. In addition to these, we are constantly exploring other opportunities as well. As the demand for growing media increases, the proportion of renewable raw materials in substrate mixtures increases, even though the total amount of peat used remains the same or may even increase.
Kekkilä-BVB’s goal is to increase the amount of substitute raw materials by 50 per cent over the next three years. The goal is important and possible to achieve with the help of new raw materials and technologies. However, due to its unique growth properties, peat is still an important ingredient in growing media used in professional horticulture. It is a valuable raw material that must be used wisely. The availability and price of peat will change in the next few years. At the same time, we want to ensure that peat is produced as responsibly as possible and that peat areas are restored after use. Our goal is to use RPP-certified peat as much as it is available to act responsibly and to meet our customers’ requirements.
You want to increase transparent communication about the value chain’s responsibility with the help of a Sustainability Compass. What does this tool entail?
In our view, sustainable growing media is one where the crop grows efficiently. The growing media must, therefore, be fit for purpose. Growing media in which the plant grows poorly is a waste of resources. We develop growth platforms based on performance, responsibility, and availability. When choosing raw materials for our growing media recipes, several aspects are taken into account. First, the raw materials or mixture’s physical, chemical, and biological performance is examined. It is important that the substrate has consistent performance and is safe to use with a low risk of contaminants. Some raw materials require processing steps, while others are relatively safe. In particular, recycled raw materials and compost have a greater chance of contamination, and this process must be managed so that the farmer does not experience crop losses.
What product development has been done about replacement growth medium materials?
Peat can stabilise the properties of other more reactive growing media materials, and it is still an essential part of many substrate mixes. Some plants can grow entirely without peat and without significantly affecting the yield. In some cases, such as champignons, peat is still needed for its antimicrobial features. The possibilities of using alternative raw materials are also strongly influenced by availability, which is often weaker than for peat. We have had good experiences with the use of sphagnum moss – the origin of peat. We use a lot of coconut, although its environmental footprint is on the same level as peat. New raw materials also require new techniques, and we do this development work together with growers. We believe that the use of peat will remain the same in volume as it is at the moment, but we are determined to grow complementary, circular raw materials alongside it, as the demand for growing media as a whole will increase worldwide. It is essential that we have optimised alternatives for different needs.
What are the prospects, and do they affect the demand for growing media and the choice of material?
Growing media suppliers play an essential role in responsible food production, growing ornamental plants, and enabling greener urban environments. The general market outlook for growing media is expected to remain positive. Global growth will be around five per cent per year, with the most considerable growth outside of Europe. New recycled raw materials and new, more efficient cultivation methods are needed to meet global demand. With growers of potted and bedding plants, and cut flowers, we are constantly developing better-growing media tailored to specific plant types. At the same time, we add circular raw materials; we aim to enhance growth for better yields. We also work with growers to match growing media with the equipment and technologies they use.
What are the strengths or competitive factors of a Finnish company that can be used to succeed in the world?
Kekkilä-BVB has strong roots in Finland, Sweden, and the Netherlands. The latter is a horticultural heartland with an impressive growing media and greenhouse cropping track record. Kekkilä and Dutch BVB Substrates were united by a thorough knowledge of growth and growing and a hundred years of experience, as well as close international and local cooperation with growers. In addition, Dutch entrepreneurship, Finnish integrity, and the challenging growing environment brought about by our geographical location have helped us find the solutions for more efficient professional horticulture. Sustainable growth has always been at the core of our business. Challenges and opportunities such as reducing carbon dioxide emissions and water, well-being through greener homes and cities, and enabling plant-based food for the world’s growing population are now our focus.
This article was published originally by FloraCulture International in their Digital magazine, May 2024 edition. Author: Timo Taulavuori.
FloraCulture International encourages the pursuit of joint activities in areas of mutual interest with national, and international societies, and organisations. Agreements have been reached between FCI and leading growers and trade associations worldwide.